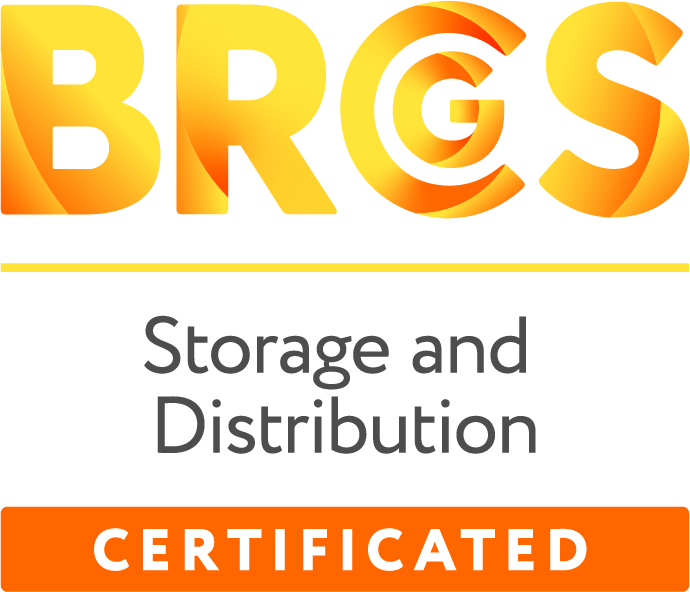
What Is Quality Control?
Quality Control (QC) is a procedure or set of procedures intended to ensure that a manufactured product or performed service adheres to a defined set of quality criteria or meets the requirements of the client or customer.
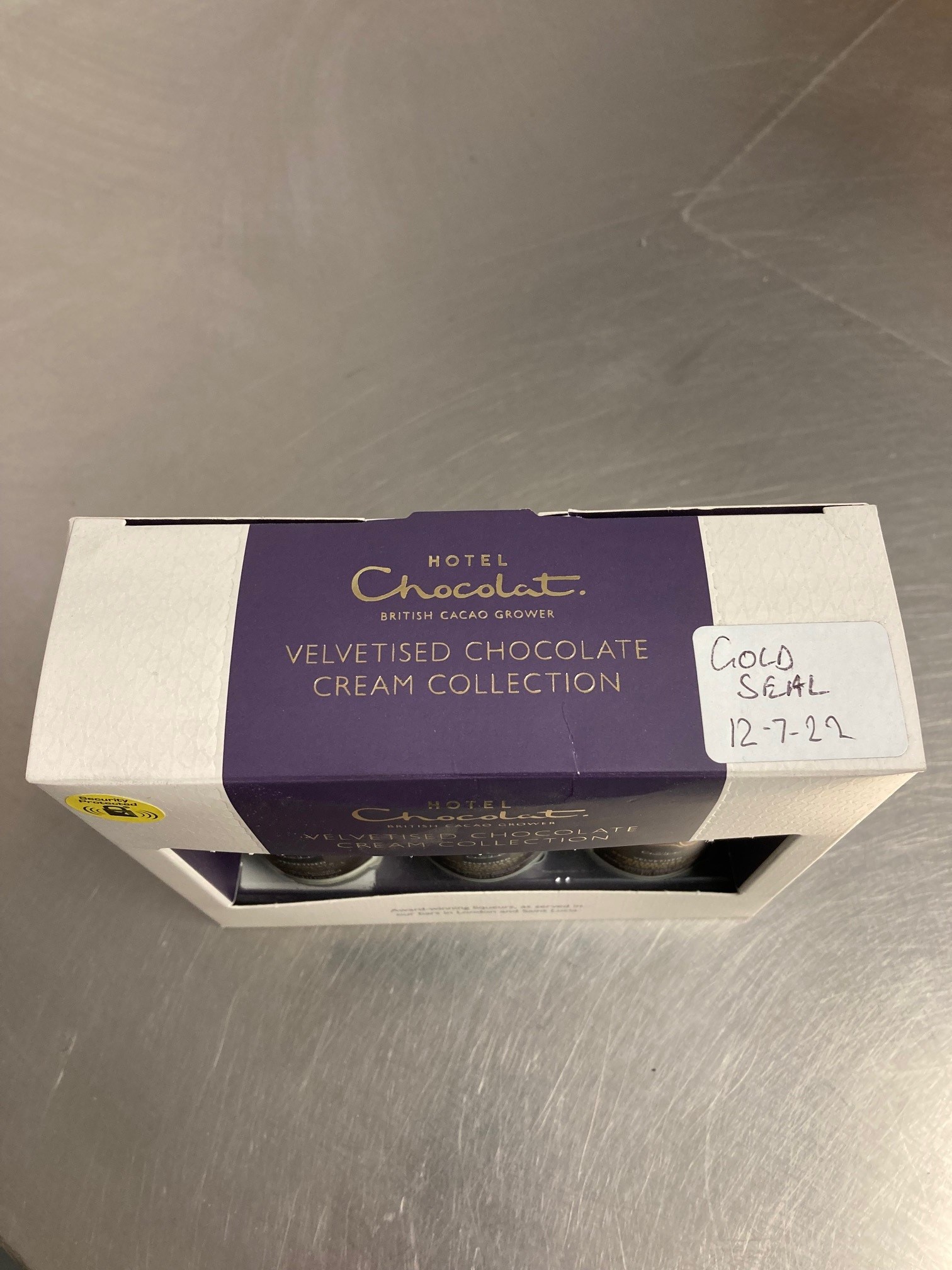
Our Approach
At Lemonpath, we work closely with both the manufacturer and the retailer. We understand the importance of a great customer shopping experience and the challenges of receiving damaged merchandise from your manufacturer. Our purpose is to ensure your merchandise is delivered to your warehouse at the highest of quality and to ensure they are ready for sale.
Products rejected by the retailer can be diverted back to our premises for immediate examination and rework. This ensures minimum delay to the product storage. Detailed reports including percentages of quality and rejection can be generated, and if required, factory liaison is also available.
Within our Contract Packing team we work closely with our Clients to agree on Gold seal standard levels of work.
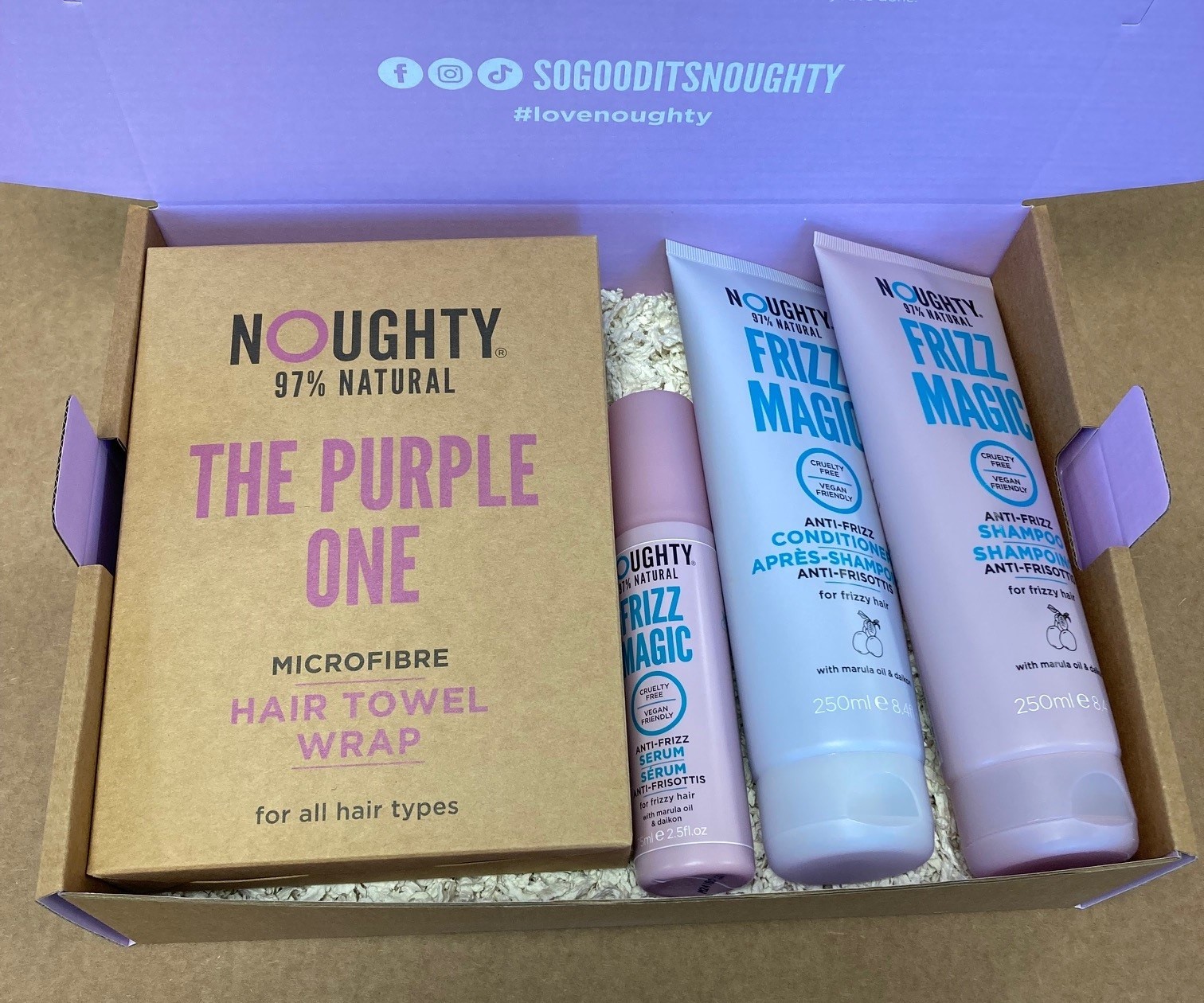
The Process
In order to ensure your products are of exceptionally high-quality, certain steps must be followed.
Case Studies
Lemonpath is proud to be the trusted partner of many companies in the UK. We’ve helped our customers grow their businesses by safely and securely getting their food products to retailers.
Let’s explore some of the ways we’ve helped our clients in the UK.
Some of the ways we’ve helped our clients...
Advantages For Retailers
- Agility
- Increases profit margin
- Saves money
- Reduces storage space and costs
- No need for extra staff
- Less stress
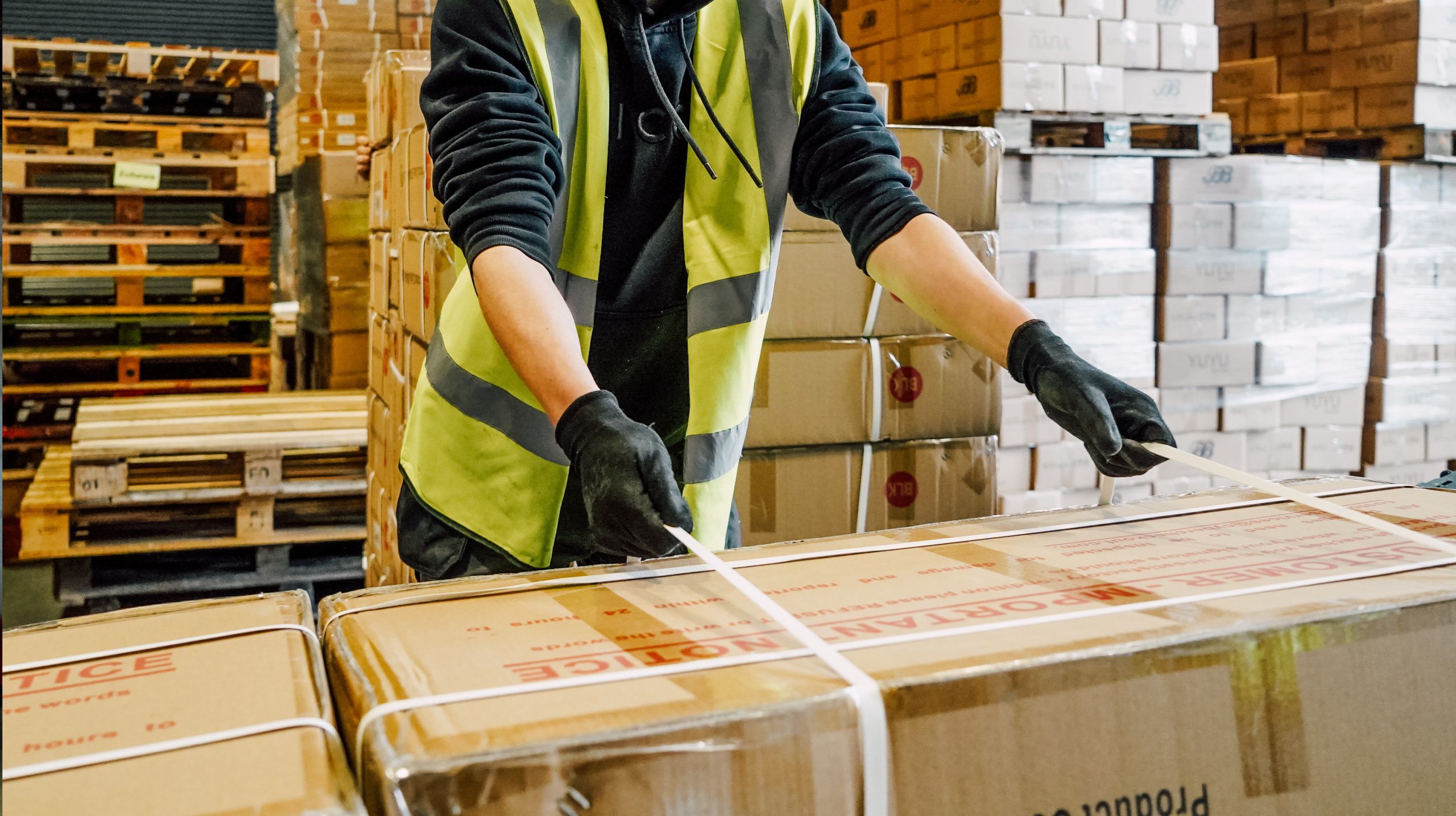